The industrial sector has cooled a bit from its post-Covid peak, when demand for these assets was white-hot in markets like California’s Inland Empire. But in a tighter market, upcycling industrial properties can make them more appealing to buyers and lessees.
Here are a few proven upcycling strategies for industrial owners and investors.
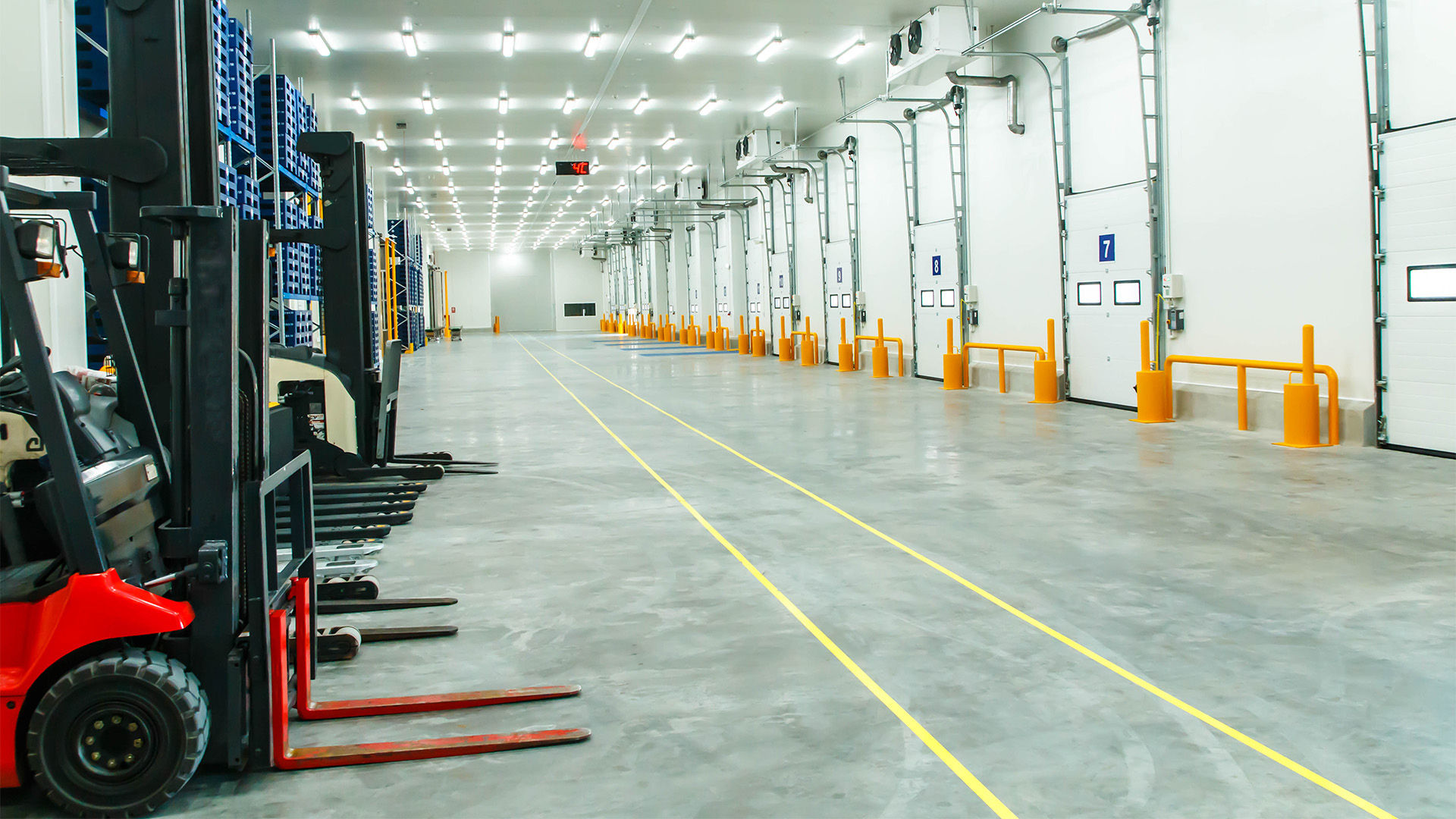
Converting to Cold Storage
Despite today’s industrial-market slowdown, observers still predict double-digit annual growth in cold storage real estate through 2030. Chalk it up to the shift to online-ordering of food, groceries and meal kits, as well as the need to refrigerate some forms of the incredibly popular GLP-1 weight-loss drugs.
Against this backdrop, an older, dry-storage industrial building potentially could be upcycled from, say, $90 per square foot in value to nearly $200 per square foot—the going rate for many cold-storage assets.
That would take some upfront investment. In a cold storage facility with freezers, it is important to maintain good thermal breaks between freezer boxes and the rest of the building. Typically, the existing floor must be replaced so that freezers can be properly isolated. Otherwise, cold can leach out from the boxes into the concrete and cause condensation and ice. In other cases, the building might need to be altered or expanded to provide adequate room for those banks of freezers.
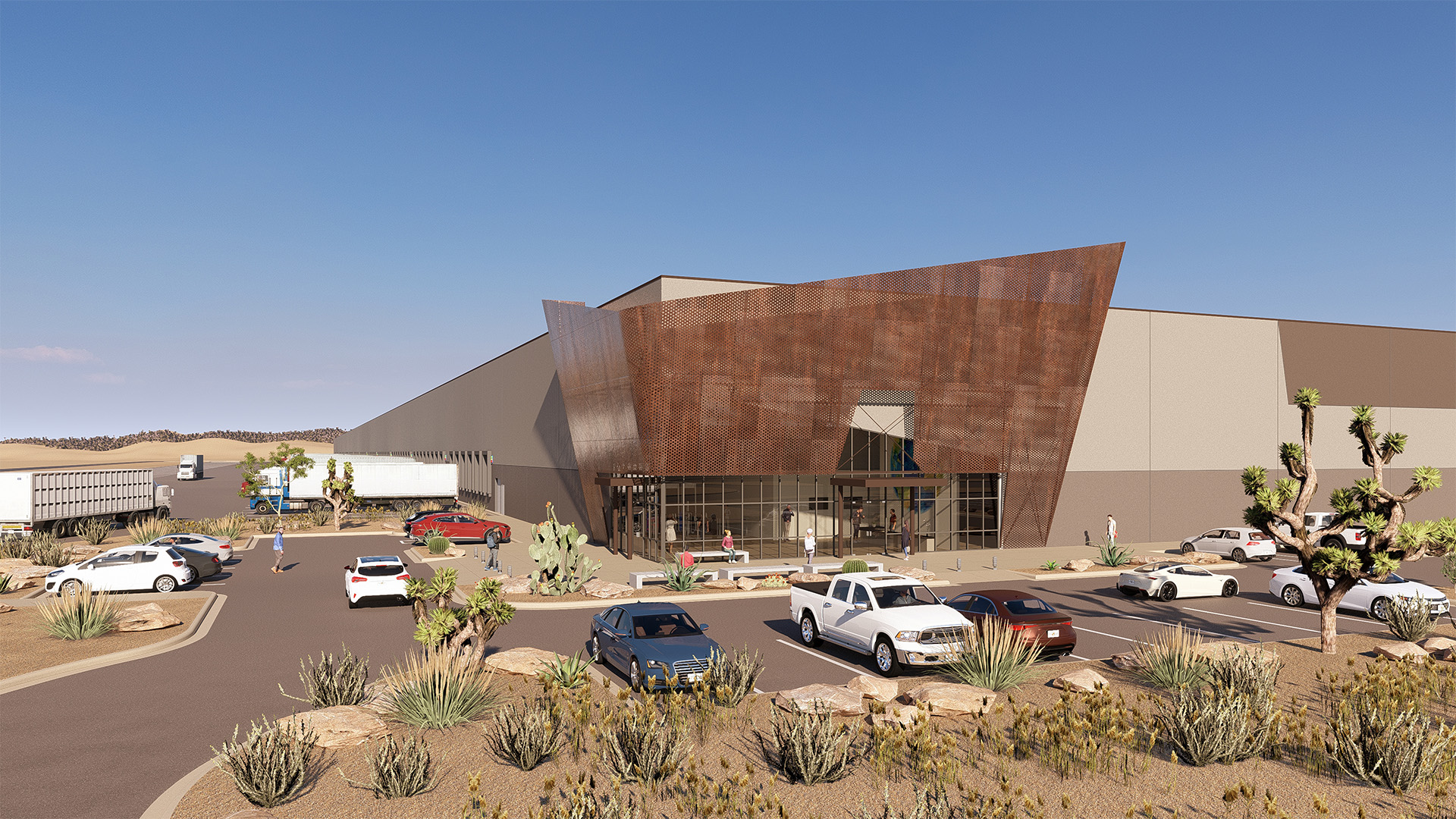
Data Center Friendly
Upcycling to another high-demand industrial use—data centers—requires an analysis of the building’s existing power capacities and future power requirements.
Many warehouses already boast access to large amounts of electricity, making them candidates for a data center conversion. An owner might also work with the municipality and electrical engineers to upgrade power capacity and make the building data center-ready. Data centers are expected to grow astronomically, driven in part by the explosion of AI and machine-learning.
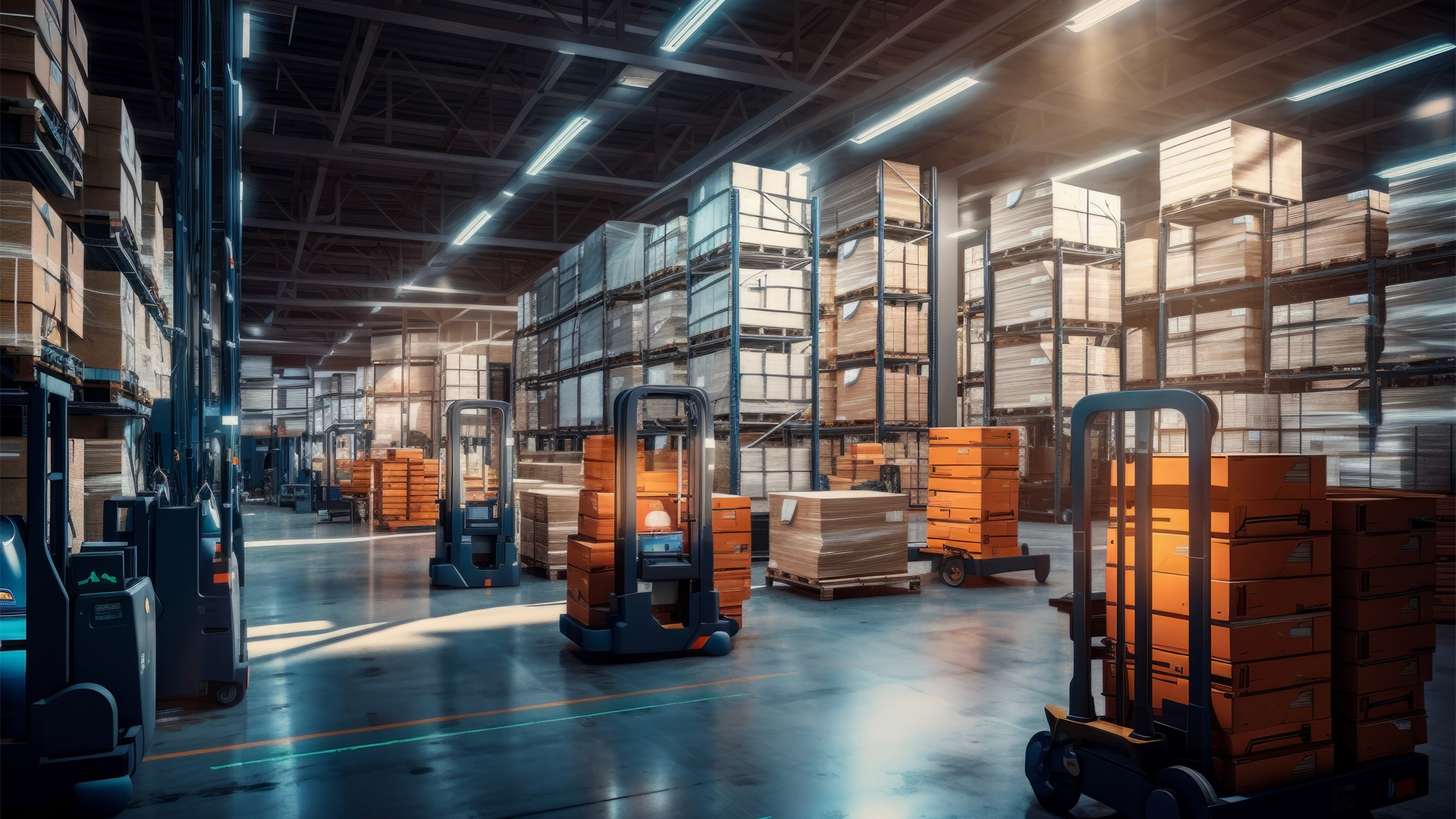
Gearing Up for Automation
A+E firms often work with owners of existing facilities on automation-related upcycling projects. For example, installing Automated Storage and Retrieval Systems (ASRS) can be a major cost-saver for occupiers, allowing them to expand their capacity without having to secure additional real estate.
With ASRS, floors must be perfectly flat. Over a given stretch of 50 to 100 feet of horizontal surface, even minute deviations—half an inch or an inch—could reduce the robots’ efficiency as they zip along on newly installed rails and tracks. Engineers sometimes X-ray or pull core samples from concrete floors to make sure they are adequately and uniformly thick. If the existing floor cannot support the additional weight, A+E firms can steer the process of putting in a replacement that meets or exceeds ASRS specs.
Lifting the roof to accommodate today’s structural clear heights might be necessary as well. Specialist companies can install new sections of steel into existing columns as the construction team carefully raises the building’s roof all at once.
Subdividing to Create New Options
In today’s tighter industrial market, fewer prospective tenants are out scouting for 500,000 or 1 million-square-foot spaces. However, the availability of smaller-format industrial spaces reportedly has reached a record low. Owners can cater to this demand by subdividing larger buildings.
The smartest approach leverages mechanical, electrical and plumbing (MEP) systems that are sub-metered for each space and give individual tenants their own controls.
Fire safety/suppression also should be a major focus of any subdivision project. This can include the use of MFL (maximum foreseeable loss) walls with specialized systems that, whenever fire-suppression is triggered, automatically drop shutters to close off openings like garage doors.
Lastly, bringing in new industrial tenants could lead to a steady stream of box trucks, higher overall traffic flow and/or the introduction of on-site containers. Engineers can help owners get a handle on any safety, site-planning and regulatory impacts.
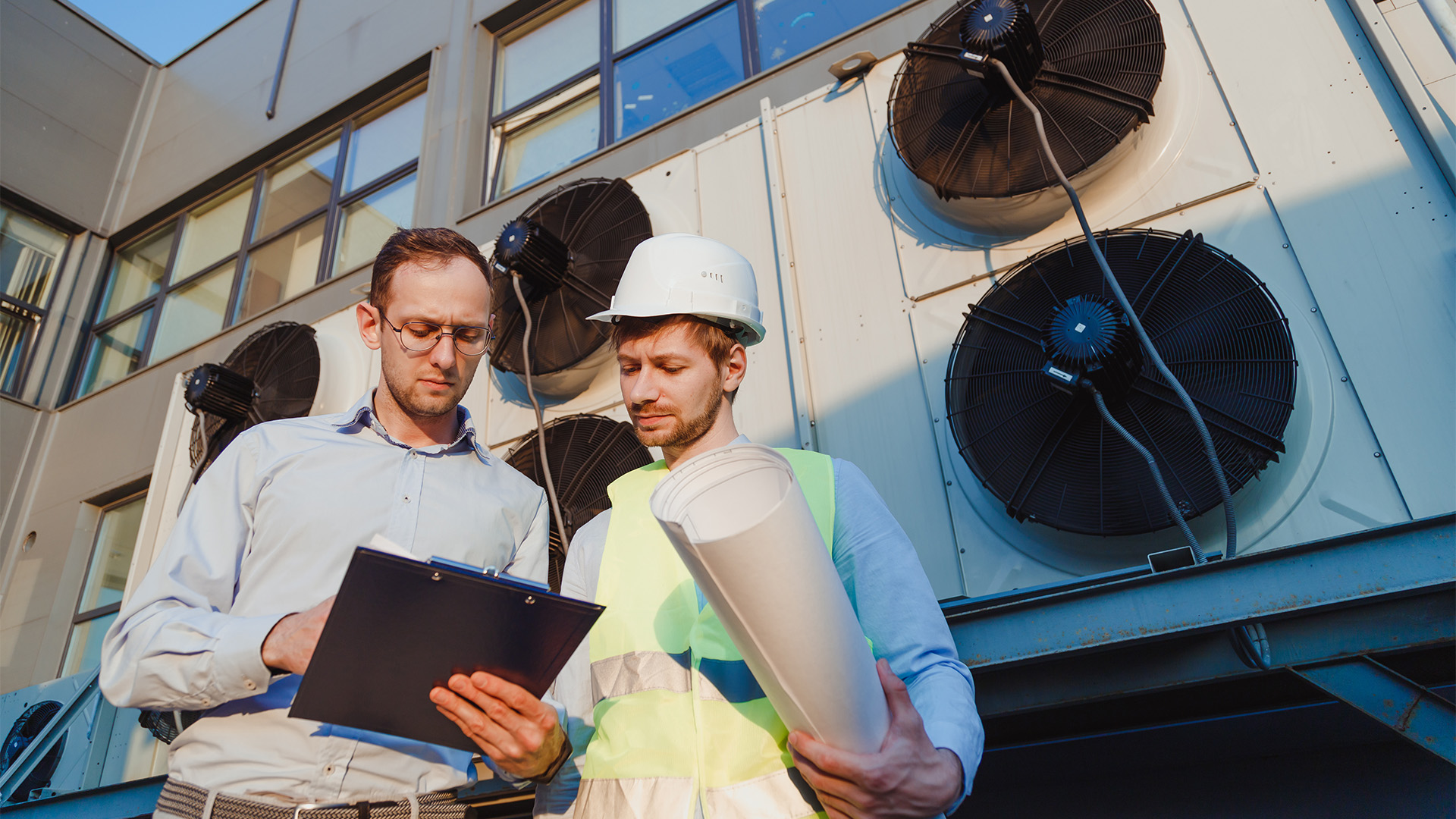
Furthering ESG goals
ESG upgrades can help industrial occupiers make progress on action items like slashing carbon-consumption or giving employees healthier, safer and more comfortable work environments. Start with a natural fit for the massive roofs of industrial warehouses—solar panels. While rooftop arrays cannot power the entire building, they can make a dent in the costs associated with charging today’s electric forklifts, chariots (personalized transportation devices for workers), yard mules and the like.
Interest is growing in on-site hydrogen generation for trucks or other equipment, or simply in making energy-efficient improvements to building insulation and other core systems.
Occasionally, industrial occupiers focused on employee comfort ask A&E firms to analyze what it would take to air condition older industrial buildings, which typically were designed to maintain less-than-comfy temperatures of 80 or 90 degrees. These projects require a detailed analysis of the building envelope and re-insulation of existing panels and the roof, along with assessments of rooftop mechanical equipment and the required addition of structural supports for a new, heavier HVAC system.
In addition, industrial owners and operators increasingly want to provide larger break rooms with spaced-out seating areas that better fit today’s post-Covid expectations around personal space, or bathrooms that are a shorter walk from any point in the building. The latter upgrade can also improve safety: Imagine having to dodge forklifts and chariots each time you crisscross a 1 million-square-foot warehouse to use a distantly located restroom.
Projects Worth Considering
Whether to invest in the marketability of any individual industrial asset is always a site- and context-specific calculation. Many U.S. warehouses were built 30 or 40 years ago on cheap real estate in what was then the city outskirts. Today, these assets sit on incredibly valuable real estate surrounded by dense development. They’re now well-positioned to offer last-mile delivery as well as short employee commutes. Upcycling them could be a smart move. Multidisciplinary A+E firms like HFA can work with owners to crunch the numbers on such projects in today’s tighter—but still strong—industrial real estate market.